What Are Heavy Mineral And Gravity Separation Process Analysis
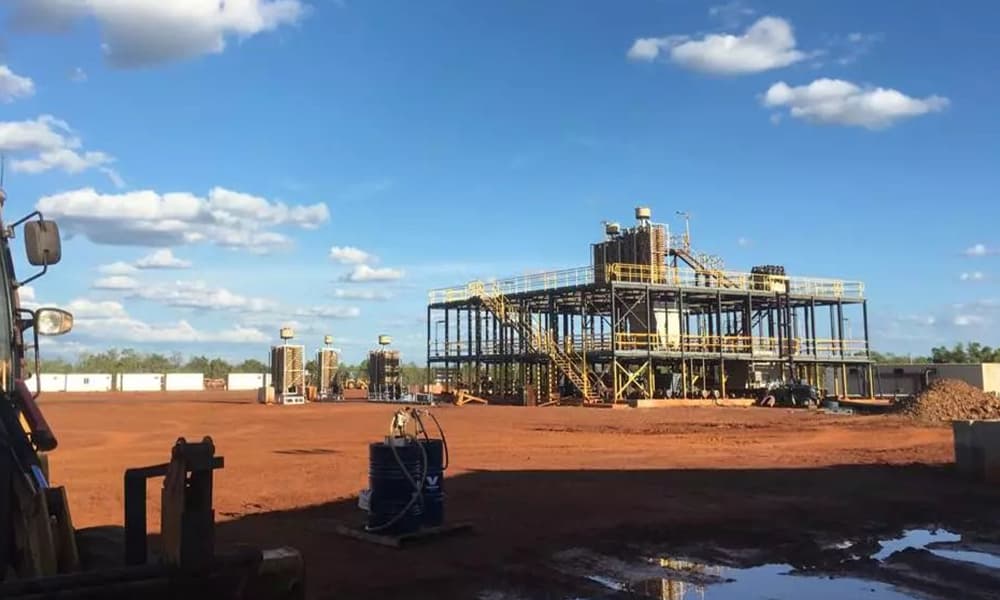
The specific process is as follows:
1. First, use a dredging pump to transport the slurryto the trommel screen hopper. The slurrydensity should be about 25-30%. The slurry pressure (flow rate) should be a manageable size.
2. The drum screen, with its 2mm mesh screen, plays a crucial role in removing waste sand larger than 2mm and discharging it directly to the nearby area. However, 0-2mm slurryfirst enters the mixing tank (2000*1500mm). Because the slurryflow rate of the trommel screen is large, the slurry needs to be stirred before being sent to the first-stage spiral group. This understanding of the equipment’s parameters empowers you to ensure efficient operation. After this, the solid materials in the slurry are evenly distributed on the spiral.
3. The slurry from the mixing tank is sent to the first-stage spiral chute group by two slurry pumps (8/6E-AH). The first-stage spiral chute has two groups (each group has 30 sets of spirals), so one group of spirals has one pump, and each group has a large distribution tank (1800*2000mm).
4. The medium slurry discharged from the first-stage spiral chute enters two slurry tanks, and then two slurry pumps (6/4D-AH) are used to transport the medium slurry to the second-stage spiral chute. The chute also has two spiral groups (10 spirals in each group), 20 groups in total), and each group has a large distribution trough (1500*1500mm)
5. The concentrate discharged from the first-stage spiral chute enters two slurry tanks, and then is sent to the third-stage spiral for final concentration using two slurry pumps (4/3C-AH). The discharged tailings enter two tailings tanks and are then sent to the tailings pile 200 meters away using two slurry pumps (6/4D-AH).
6. The concentrate discharged from the second-stage spiral chute enters a slurry tank and then uses a slurry pump (3/2C-AH) to send the concentrate to the third-stage spiral large distribution tank (1000*1200mm). The discharged tailings enter a slurrytank and are then sent to tailings pile 200 meters away using a slurrypump (6/4D-AH).
7. The final heavy mineral concentrate product discharged from the third-stage spiral chute enters a slurry tank. Then, a slurry pump (1.5/1C-HH) delivers the concentrate to a ground concentrate pile 300 meters away.
8. We have designed the process to be adaptable. We will consider installing some water supply pipes to add extra water to each spiral. When the slurry separation effect is not good and the slurry density is too high, we have the flexibility to add a little extra water to the spiral. Whether to add additional water depends on the actual separation effect of the spiral and the ore conditions, and is mainly used as a backup. This flexibility in the process should give you confidence in handling variations in the operation.